リーマを正しく使用するための選定ポイントとは?
リーマとはどのような工具?
リーマとは、ドリルなどで開けられた穴の寸法精度、面粗度、幾何公差を整える為の、仕上げ加工用の切削工具です。リーマは、ドリルと違い、リーマのみで穴を開けることはできません。開けられた穴に高い精度の仕上げを行うために用いられます。
リーマを正しく使用するためのポイントとは?
リーマを適切に使用するには、①被加工物の材料特性を知ること、②下穴寸法と仕上がり寸法の設定、③使用する機械の仕様(剛性、切削条件)、④切りくずの排出性、⑤潤滑方法といった環境がどうなっているかを把握する必要があります。その上で、正しい工具設計を行うことでより高い効果を得ることが出来ます。
リーマの設計ポイントとは?
設計のポイントは7つあり、①工具材質、②寸法設定、③振れ精度、④ねじれ、⑤食い付き形状、⑥マージン、⑦刃数です。
①工具材質
被加工物や使用機械の加工条件に合わせて選定をします。主に、ハイスと超硬の2種類の材質が挙げられます。この他にも、特殊な条件下で使用されるサーメットやダイヤモンドもあります。ハイスは超硬と比較すると、靭性が高く耐折損性や耐欠損性に優れている反面、硬度が低い(HRc60~68前後)ことから高硬度材の加工には向かず、耐熱性も劣る為、高い加工条件下での使用には向きません。一方で超硬は、硬度が高い(HRA90~94前後)ことで靭性が低く、衝撃によって折損や欠損することがありますが、要求精度が厳しく工具のたわみを抑えたい場合には望ましいです。
②寸法設定
下穴の寸法と仕上がり寸法によって決まります。リーマでの切削しろは、一般的に径で0.05~0.3mm程度と言われています。これ以上の切削しろは、切削抵抗が大きくなり、熱損傷や切りくずの噛み込みにより仕上げ面が荒れてしまう可能性があります。
③振れ精度
径や長さによって異なってきますが、一般的に円周振れでレンジ5µm以下に仕上がっています。
④ねじれ
リーマの回転方向が右回転である前提としたとき、同じ方向にねじれている「右ねじれ」、反対方向にねじれている「左ねじれ」、ねじれていない「直刃」の3種類があります。右回転で使用されることから刃は右刃になる為、「右刃右ねじれ」「右刃左ねじれ」「右直刃」と表現されます。一般的には「右刃右ねじれ」「右直刃」に設定されます。「右刃左ねじれ」は、食い付き部の切削性が下がってしまい切削抵抗が増大するデメリットがありますが、加工後の拡大しろが小さいことから穴の寸法精度が厳しい際に設定することがあります。また、切りくずがリーマの進行方向に対して排出されるため、通り穴である必要があります。
⑤食い付き形状
加工精度に大きな影響を与えます。食い付き角度によって、スラスト抵抗や切削トルク、仕上げ面粗さ、寸法精度が変化します。食い付き角度が小さい場合には、スラスト抵抗が小さくなり、切りくずの厚みは薄くなります。その結果、仕上げ面粗さが向上し、加工後の拡大しろも小さくなります。しかし、喰い付き角度が小さく、取りしろが多いと、ワークに接触する切れ刃の長さが長くなり、幅の広い切りくずが生成されることで排出が上手く行かず、加工面に擦り傷等の影響が出ることがある為、適切な取りしろの設定が必要です。また、食い付き角度が小さいと、リーマが下穴に沿って入っていこうとし易くなります。つまり、下穴の加工精度に依存する傾向にあります。その為、真直度や真円度の修正をリーマで行う場合には食い付き角度を大きくして、リーマの切削作用を大きくする必要があります。一般的には45°に設定されることが多いですが、これは過去の経験や知見において、仕上げ面粗さや切削抵抗、工具の摩耗状態のバランスが一番取れていることから選ばれたと考えられています。
⑥マージン
穴に面で接触しますので寸法精度、面粗度に大きな影響を与えます。小さくすることで切削抵抗や切削トルクは低減できますが、バニッシュ効果は減少します。一方で大きくすることで、バニッシュ効果の増大だけでなくガイドとしての役割が大きくなり、真円度の改善やビビり対策に繋がりますが、大きくし過ぎると切削抵抗が増大して摩擦熱が発生することでの溶着のリスクや加工精度の悪化に繋がります。
⑦刃数
3~8枚刃が一般的です。刃数が増えるほど接点が増え真円に近くなり、マージンも増えることでバニッシュ効果が増大しますが、増やし過ぎると切りくずの排出性が低下し、切りくずのつまりや噛み込みが発生します。また、切削トルクの増大にも繋がります。
当社の工具事例をご紹介
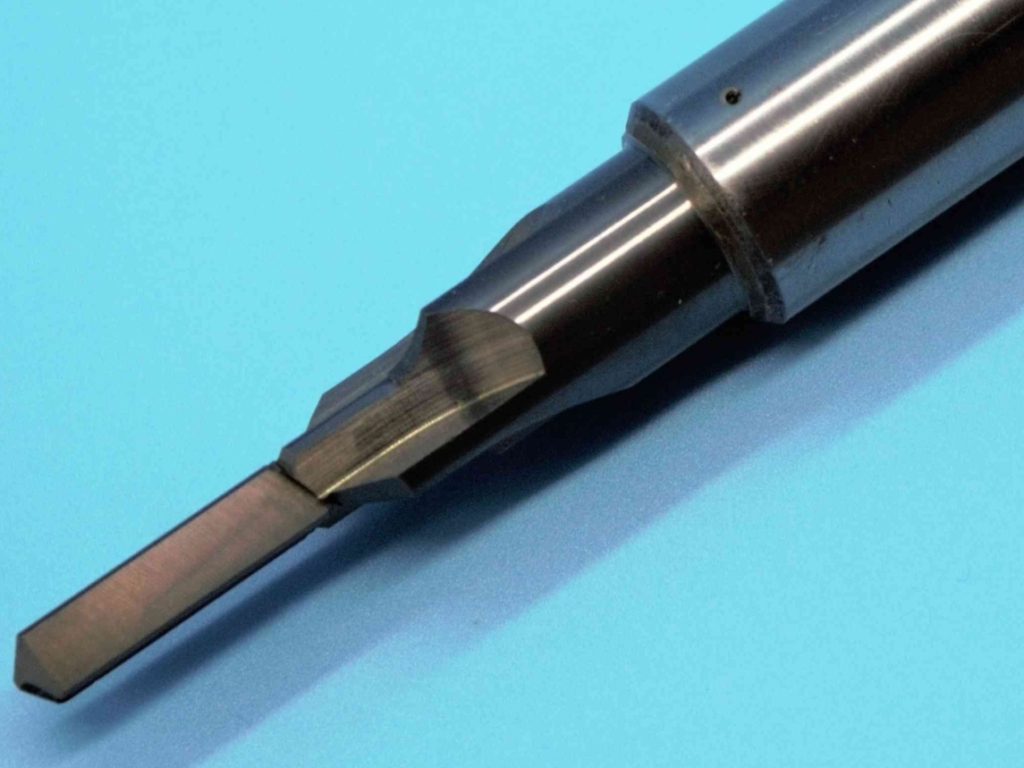
段付きリーマ
段付きリーマは、多段穴仕上げに用いられるリーマです。スパイラルリーマとは違い、名前の通り刃部が段付き形状になっていることにより、径が異なる複数の下穴を一度に加工することができます。これにより、加工工程が集約化を実現できます。段付きリーマを製作するためには、加工する穴の寸法に合わせた各段の径や長さを決め、特注での製作が必要となります。そのため、試作品などの加工で使用されることは少なく、多くは量産加工をする際に使用されます。これにより、段付きリーマのメリットを最大限に活かすことができ、加工工程の集約化によるコストダウンを実現できます。
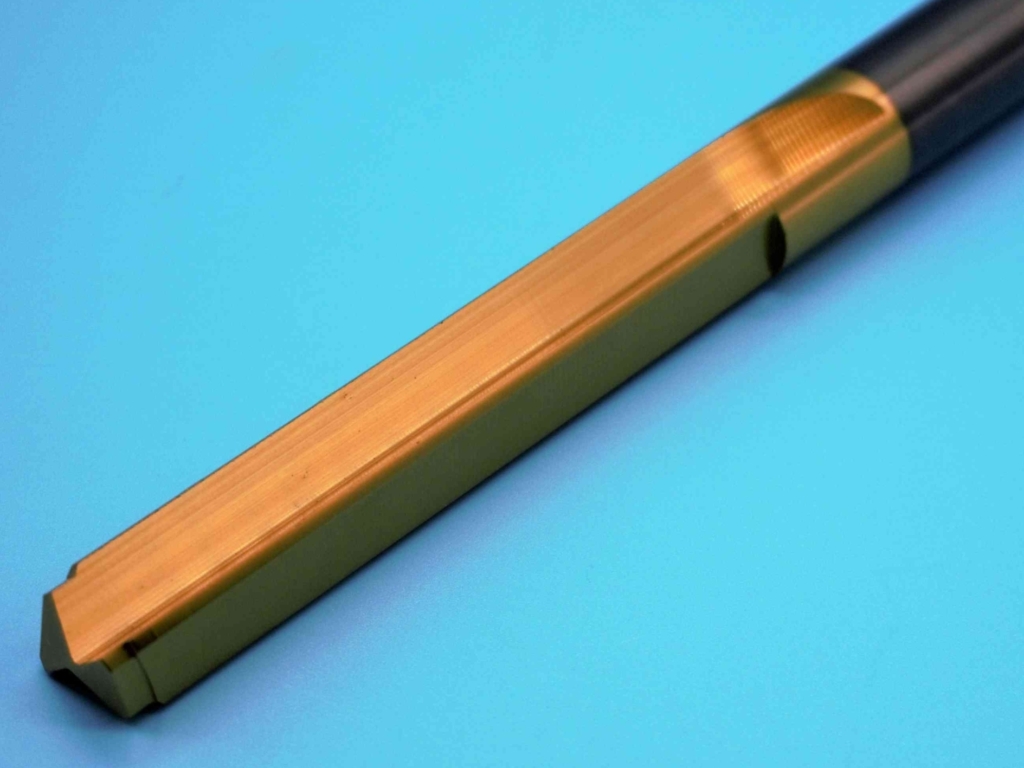
バニシングリーマ
バニシングリーマは、下穴の加工表面に面粗度を向上させるバニッシュ効果を与えるリーマです。スパイラルリーマとは違い、段付き形状により多段穴仕上げ加工を一度に行うことが出来ます。これにより、加工工程の集約を実現できます。バニシングリーマの特徴として、ステップの肩に2面のストレート刃と、外周に4面の円筒状のバニッシュマージンを持っています。バニシングリーマは、2面のストレート刃で加工面を削り、4面のバニッシュマージンにより加工面をすり潰すことにより、面粗度を向上させます。また、バニシングリーマは、溶解ハイス、粉末ハイス、超硬合金などで製作され、強度が高いアルミや鋳物材質などの仕上げ加工に適しております。
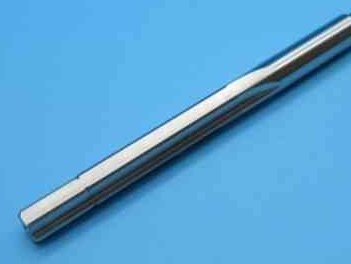
パイロット付リーマ
こちらは自動車業界で使用されるサイズがφ7.988×φ6.35×114のハイス製パイロット付リーマです。ワークの面粗度を改善したいとのことでご依頼をいただきました。特殊精密切削工具.comにおいては面精度の悪化を誘発しているねじれ角やマージンの見直したところ、面粗度が良くなり、メーカーでの品質検査も合格出来ました。当社ではリーマの設計の要であるねじれ角、マージンをワーク材質や加工条件に合わせて設定するノウハウを多数保有しており、過去製造したリーマは2つとして同じ工具はなく、すべてお客様のご要望に沿って開発・製造したオーダーメイド工具です。ぜひワークの面精度でお悩みがございましたら、お気軽にご連絡ください。
精密切削工具の製作なら特殊精密切削工具.comにお任せ下さい!
今回はリーマの選定ポイントについてご紹介をさせていただきました。リーマを適切に使用するには、①被加工物の材料特性を知ること、②下穴寸法と仕上がり寸法の設定、③使用する機械の仕様(剛性、切削条件)、④切りくずの排出性、⑤潤滑方法といった環境がどうなっているかを把握する必要があります。その上で、正しい工具設計を行うことでより高い効果を得ることが出来ます。
当社では創業から84年以上、お客様のご要望に合わせてオーダーメードの工具を開発・製造してまいりました。お客様それぞれに世界一の究極の逸品の工具を作り上げることをモットーに最先端設備を揃えており、高精度な加工を実現する環境を整えてまいりました。工業界から医療業界と「人体から宇宙まで」幅広く、精度が必要な工具の納品実績が多数ございます。
切削工具にお困りの方は、特殊精密切削工具.comまでお問い合わせください!
最後まで読んでいただき、ありがとうございました!