ドリルの加工時に起きるトラブルとその対策について
はじめに
機械加工に従事する多くの方々にとって欠かせない切削工具。しかし、切削工具を使用する上で、チッピングや折損、切りくずの詰まり等のトラブルが起きてしまう場合があります。トラブルに対し、最適な対策をしなければ加工コストの増加のみならず、加工品質の低下に繋がりかねません。今回は、ドリルのトラブルとそれぞれへの対策について説明します。
ドリルは、どのような工具?
ドリルとは、被削材に穴を開けるための切削工具です。ドリルを回転させ、先端の切れ刃を被削材に接触させることにより、切り屑を排出しながら穴を開けていきます。ドリルの使用用途は、金属材料を加工するだけではなく、ガラスなどの脆性材料、プラスチックやアクリルなどの樹脂材料、木工材料、土木の現場で使用されるコンクリートの加工、及び医療用として人骨を削る際にも用いられています。
ドリルに求められる特性は、①狙ったところに真っ直ぐに穴を開けられること(求心性)、②開いた穴がより正円に近いこと(真円度、振れ精度)、③切りくずの処理がスムーズであること(排出性)、④切削熱に強いこと(耐熱性)、⑤長期間使用出来ること(高寿命、耐摩耗性)が挙げられます。したがって、ドリルを製作する際は、これらの特性を満たすための工具設計と最適な工具材料の選定が重要となります。
>>ドリルの基礎知識・各部の名称【切削工具の基礎知識シリーズ】
ドリルに求められることとは?
ドリルに求められる特性は、狙ったところに真っ直ぐに穴を開けられること(求心性)、開いた穴がより正円に近いこと(真円度、振れ精度)、切りくずの処理がスムーズであること(排出性)、切削熱に強いこと(耐熱性)、長期間使用出来ること(高寿命、耐摩耗性)が挙げられます。これらを満たすためには、ワークのことを理解し、仕上がり寸法や使用する機械、環境に合わせて設計する必要があります。しかし、誤った設計になっていると、ドリルが異常摩耗を起こしたり折損してしまったり、またワークを傷つけてしまうと言ったトラブルを起こしてしまいます。
>>技術コラム『ドリル刃を精密加工する際のポイントについて』はこちら
ドリルにおいて発生するトラブル
ドリルにおけるトラブルには大きく分けて2種類あり、1.摩耗、2.折損、3.チッピングといった工具側に起きる問題と、4.穴が曲がってしまう、倒れてしまう、5.穴が広がってしまう、6.加工面が荒れてしまうと言ったワーク側に起きる問題です。
1.異常摩耗
ドリルの摩耗は切削性の低下に繋がります。原因として、被削材に対して工具材質が合っていない、もしくは加工条件が合っていないことが多いです。被削材の硬度と同程度の硬度の工具を使用しても切削することは出来ません。また、工具材質に合った適正な切削速度、送りで加工を行わないと能力以上の仕事をドリルにさせてしまい、ドリルは摩耗してしまいます。対策として、工具材質の見直し、コーティングの付加、加工条件の見直しを行うことで解消できます。この他に、切りくずの排出が適切に行えていない可能性があります。適切に行えていないと、切削抵抗となってしまい、切れ味の低下や切削熱の影響による熱損傷が起きやすくなってしまいます。対策として、適切なシンニングを設けること、ねじれ角の見直し、また切れ刃にニックを設けて切りくずを分断させ排出性を向上させることが挙げられます。特にシンニングは、先端付近の切れ刃が無いチゼル部に切れ刃を設ける加工で、スラスト抵抗を減少させ、食い付きと切削性を向上させます。
2.折損
原因は、強度がワークに対して不足していることや、靭性が不足していることが考えられます。対策として、強度を増すためには心厚(ウェブ厚)を大きくすることや溝幅比を見直して工具断面積を大きくすることが挙げられます。その際、刃溝が浅くなり過ぎてしまい、切りくずの排出性が悪くならないよう注意が必要です。また、溝長を不必要に長くせず、切りくずの排出が適切に行える範囲で短くすることも挙げられます。靭性が不足している場合には、硬度を少し落とし、靭性のある材料を選ぶ必要があります。例えば、超硬製を使用している場合には、ハイス製に切り替えることや、超硬の中でもタングステンカーバイドの粒径が小さく靭性の高い超硬(超微粒子、超々微粒子)に切り替えるということが有効です。
3.チッピング
原因は、送りや回転数が高すぎることや、刃先の強度が不足していること、冷却が適切に行われず構成刃先の生成、脱落が繰り返されることが考えられます。対策として、刃1回転当たりの送りから逃げ角を見直し、必要最低限の逃がしにします。また、冷却方法を見直し、クーラントの掛け方や、外部給油から内部給油への変更が挙げられます。
4.穴が曲がってしまう(真直度の不良)、穴が倒れてしまう(直角度の不良)
原因として、工具剛性の不足、工具の摩耗が進行していること、切れ刃のリップハイトがずれていることが考えられます。リップハイトのズレは、ドリルの再研磨時に起きやすく、刃先が工具中心からずれてしまったり、先端角が左右非対称になってしまったりすることで直進性に影響が出ます。また、センター穴の加工が十分にされていないと、より上記の影響を受けてしまいますので、センター穴加工は適切に行っておく必要があります。対策として、工具材質の見直しや、シャンク径を大きくすること、再研磨時に2枚の刃を同じ再研磨量で再研磨することが挙げられます。
5.穴が広がってしまう
原因として、穴加工初期でドリルの食い付きが悪く振れが発生してしまっていることや、ドリルを機械に取り付けた際に、適切に取り付けられておらず、既に振れが発生している可能性があります。対策として、被削材や加工条件に合わせたドリルのシンニング形状を見直すことや、ツーリング、ドリルの振れを再度確認することで対策が挙げられます。
6.加工面が荒れてしまう
原因として、適切な加工条件で加工されていないことや、刃が摩耗してしまい、切削性が低下していることが挙げられます。対策として、加工条件の見直し、再研磨の実施が挙げられます。ドリルには被削材によって1刃当たりが加工できる切削能力がある程度決まっております。また、送りと切削速度(回転数)が適切なバランスで加工をされていないと、刃の摩耗が進行し、加工面を荒らします。
当社の工具事例をご紹介
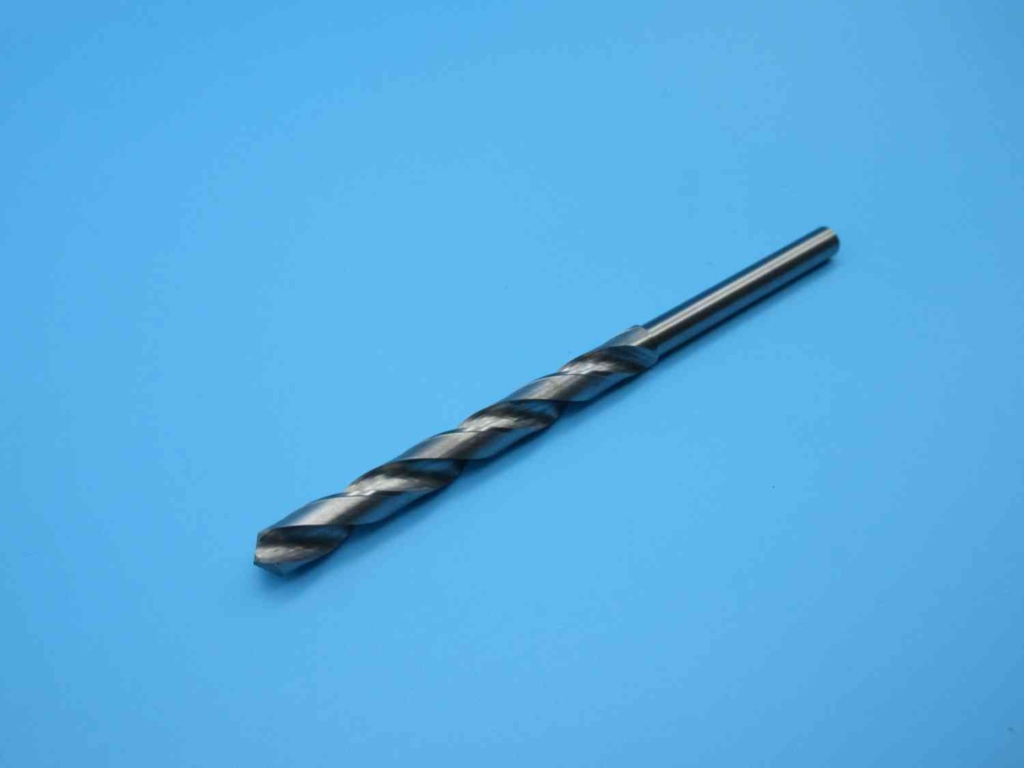
超硬ドリル
自動車業界で使用されるサイズがφ7.67×125の超硬製ドリルです。お客様よりドリルで加工した穴径にバラツキが発生するために改善提案をお願いしたいとご依頼をいただきました。特殊精密切削工具.comではお客様の使用しているドリルにリップハイトの差が大きく発生していたことを確認し、リップハイトの差が無いドリルを納入しました。当社ご提案工具を使用した結果、安定した加工が出来ました。
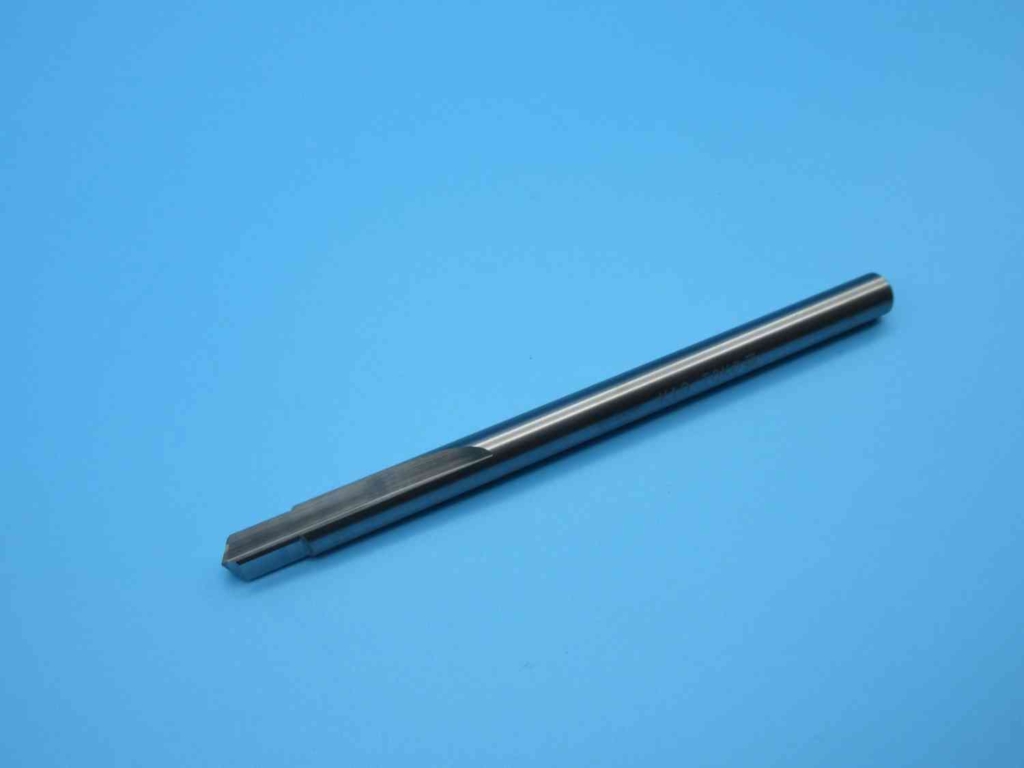
バニシングドリル
インフラ業界で使用されるサイズがφ8×120の超硬製バニシングドリルです。お客様より加工面に傷がついてしまうために改善提案のご依頼をいただきました。特殊精密切削工具.comでは従来の使用工具より切屑の排出性と切削油のかかりを良くするため、バニッシングドリルの溝長を伸ばしてご提案をしました。当社ご提案工具を使用した結果、不良品の発生が50%削減出来ました。
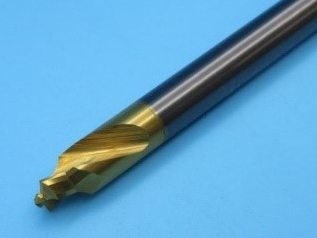
段付ドリル
輸送用機器業界で使用されるサイズがφ8×70の超硬製段付きドリルです。お客様で使用されていた段付きドリルでは先端部が頻繁に折損していたため、折損を抑えたいとご依頼いただきました。特殊精密切削工具.comで切屑の排出性向上を狙い、シンニング形状を見直しました。すると先端部の折損が無くなり、寿命まで工具を使用出来るようになりました。折損の原因は切屑詰まりによる場合やチッピングによる場合など、様々な原因が考えられます。今回では切屑詰まりによる工具の回転不足による折損であるために、工具の中心部に刃を付けるシンニング対策を実施することで、切屑の逃げ道を作り折損を防いでいます。
トラブルを根本的に解決するためには
軸物工具におけるトラブルを列挙しましたが、2つ以上のトラブルが同時に発生してしまうという方もおられると思います。加えて、現状のトラブルを全て解決しようとすると、何から取り組めば良いか分からなくなってしまいかねません。これを根本的に解決するためには、「切削理論」と「材料特性」を熟知している特殊精密切削工具.comにご相談ください。
当社では創業から84年以上、お客様のご要望に合わせてオーダーメードの工具を開発・製造してまいりました。お客様それぞれに世界一の究極の逸品の工具を作り上げることをモットーに最先端設備を揃えており、高精度な加工を実現する環境を整えてまいりました。工業界から医療業界と「人体から宇宙まで」幅広く、精度が必要な工具の納品実績が多数ございます。
切削工具にお困りの方は、特殊精密切削工具.comまでお問い合わせください!
最後まで読んでいただき、ありがとうございました!