ドリル刃を精密加工する際のポイントについて
ドリルとはどのような工具?
ドリルとは、被削材に穴を開けるための切削工具です。ドリルを回転させ、先端の切れ刃を被削材に接触させることにより、切り屑を排出しながら穴を開けていきます。ドリルの使用用途は、金属材料を加工するだけではなく、ガラスなどの脆性材料、プラスチックやアクリルなどの樹脂材料、木工材料、土木の現場で使用されるコンクリートの加工、及び医療用として人骨を削る際にも用いられています。ドリルはJIS(日本工業規格)に準拠した分類方法で①刃部材料及び表面処理、②構造、③シャンクの形態、④機能又は用途の計4種類に分類されております。
ドリルに求められる特性は、①狙ったところに真っ直ぐに穴を開けられること(求心性)、②開いた穴がより正円に近いこと(真円度、振れ精度)、③切りくずの処理がスムーズであること(排出性)、④切削熱に強いこと(耐熱性)、⑤長期間使用出来ること(高寿命、耐摩耗性)が挙げられます。したがって、ドリルを製作する際は、これらの特性を満たすための工具設計と最適な工具材料の選定が重要となります。
>>ドリルの基礎知識・各部の名称【切削工具の基礎知識シリーズ】
ドリルに要求される特性とそれに伴い使用される材質とは?
まず一般的に工具は、使用状況や環境によって求められる特性が異なります。上記でご紹介したドリルの分類方法に合わせて、最適な材料の選定が重要となります。切削工具の場合には、耐摩耗性が重要となります。加えて切削加工の際には刃先の先端が高温状態となり、工具寿命の短命化や熱膨張による精度の低下が挙げられます。したがって、高温状態でも硬さが低下しないかつ構成刃先を生じにくいことが要求されます。
これらの特性を満たすために、工具材料として最も汎用的に選ばれているのはハイスと超硬合金の2種類です。ハイスと超硬合金では靭性と硬度による比較がされており、ハイスは硬度で劣りますが、靭性があるために刃が欠けにくいという面がございます。一方で、超硬合金は靭性で劣りますが、硬度に優れるために工具の歪みやしなりがでにくく、高精度で美しい仕上げ面で加工が可能です。
ドリルを製作する上で注意するポイントとは?
ドリルを製作する上で注意すべきことは、①切れ味と②切屑の排出③求心性の3点を重視した設計が必要となります。
切れ味
切れ味の良いドリルを設計するためには、被削材に応じた先端角、逃げ角、シンニング、ねじれ角・外周・溝の深さを設定することが重要です。
①ねじれ角はねじれ角が大きいほど、切れ刃が鋭利になり切れ味が良くなるため切削抵抗が小さくなります。ただし、切れ刃の強度は低くなるため、チッピングや欠けが生じやすくなります。 標準的なドリルのねじれ角は20°~30°であるために、切れ味を良くする際にはねじれ角を大きく設定します。
②ドリルのねじれ角は、ドリルの外周とリードで決定されます。ねじれ溝がぐるっと一周して同じ線上に表れる長さをリードと言います。そのねじれている角度がねじれ角となります。計算式で表すとtanθ(θはねじれ角度)=(ドリル直径D×π)/リード⇒θ=tan⁻¹(Dπ/リード)となります。
切屑の排出
切屑の排出は、ねじれ角・すくい角・面粗度・溝幅比、ウェブ厚の5つの条件で変化するので、装着する工作機械とその加工方法に合わせた設計が重要です。切屑排出性を高めるためには、下記の各種項目を大小させることが重要ですが、全て設計上での他の要素との兼ね合いが前提となります。
①ねじれ角はその名の通り、刃のねじれの角度を指します。ねじれ角が大きい場合には切削時の切削抵抗が少ないために切屑自体が薄くなります。切屑が薄い場合には切屑の排出性が高まります。しかし、排出するための距離が長くなるデメリットがあります。
②すくい角は切れ刃と被削材の基準面に対するすくい面の傾きを表します。すくい角はねじれ角と相対的な関係性を持っています。したがって切屑の排出性を高める場合には、すくい角を強くすると低い切削抵抗で切屑の排出性を高めます。
③面粗度を向上させる、特に溝部の面粗度を向上させる事で、滑り性がよくなり、切屑がスムーズに排出されます。
④溝幅比とはドリルの先端におけるランドの角(θ1)に対する溝の角(θ2)の比のことです。溝幅比=θ2/θ1の式で表されますので、溝幅比が小さいと剛性は高いが切屑の排出が悪くなり、溝幅比が大きいと剛性は下がりますが、切屑の排出は良くなります。一般的に、靭性が低い超硬は溝幅比を小さめに、靭性が高いハイスは溝幅比を大きめに設定されています。
⑤ウェブ厚は別名芯厚と呼ばれており、刃具の中心から外周溝の底までの太さを指します。このウェブ厚が太い場合、工具断面積が広くなるために剛性が高まりますが、一方でチップポケットは狭くなるために切屑の排出性が悪くなります。そのためにウェブ厚を小さく設計することが重要となります。
求心性
求心性とは、ドリルが加工している際に、あけたい穴の中心を求めていく性能のことを言います。ドリルが剛体であるとドリルの先端中心とシャンク端面が同じ軌跡を描きます。つまり、主軸の回転中心から見た切れ刃の向きは常に一定です。しかし、ドリルが軟体で変形を伴う場合にはドリルの先端とシャンクの端面は同じ軌道を描くことがなく、穴が曲がるなどの現象が発生します。これらの要因を解消する求心性を上げるために、剛性を上げた設計をすると共に被削材の材質によるが左右の刃のばらつきを抑えた設計であるリップハイトが重要です。またチゼルエッジを小さくするためにシンニング加工を施すことも効果的です。ドリルのすくい角は中心部に近づくにつれて小さく、負のすくい角となり、切削抵抗力を強めて切れ味が非常に悪くなります。シンニング加工することで、すくい角に切れ刃ができて、切削抵抗を抑え、安定的な切り屑の排出を実現することが可能となります。
当社の工具事例をご紹介
-1-1024x819.jpg)
段付きドリルは刃径が2段以上あり、ワークに対して1回の加工で2段、3段の異なる径の穴を開けられる加工が可能なドリルです。段付きであるため1工程で面取りまで加工が完了できる為、同軸度が保証される点と複数のドリルを使用する事が無い為、サイクルタイムの短縮を実現することが出来ます。ただ通常の段付きドリルは先端側のねじれ角が弱くなり切れ味・切屑の排出性の低下や面相度の悪化、寿命の短命化を引き起こします。そこで当社では、ねじれ角度差を小さくする場合や最適なコーティング方法にてこれらの問題を解消しております。
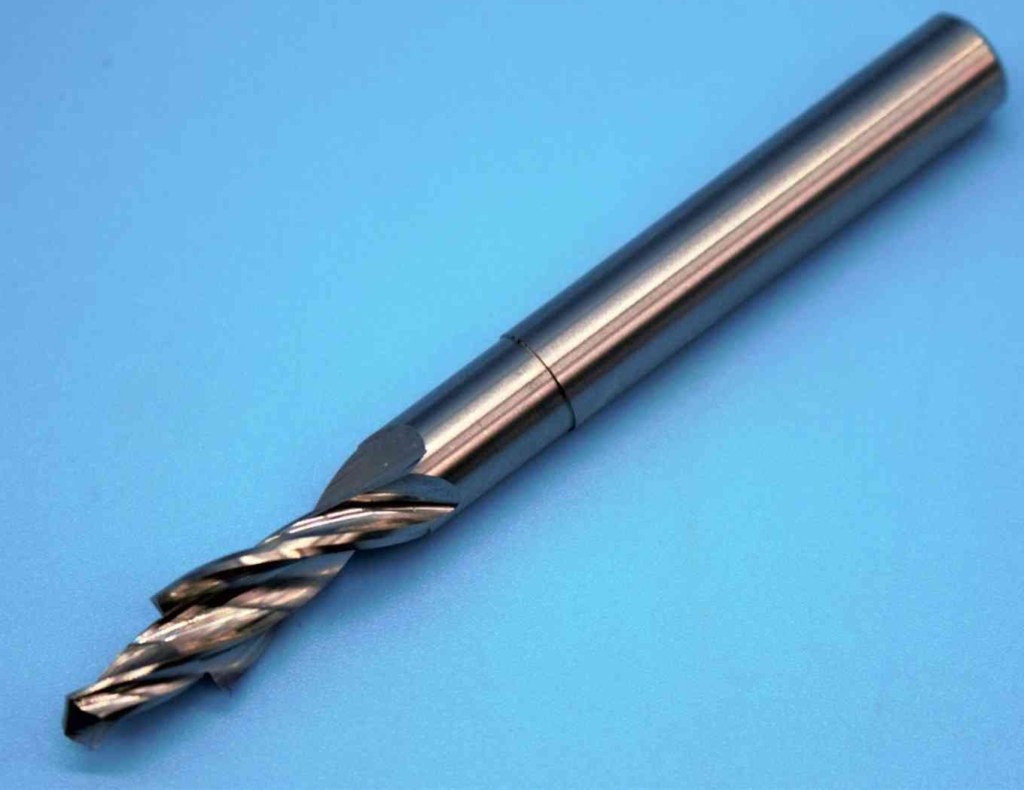
こちらのサブランドドリルは、大径に小径部の溝を持っていることで再研磨回数を増やすことができます。通常の段付ドリルは、再研磨時で小径部のステップ長が短くなると廃却になります。しかしサブランドドリルは、大径に小径部の溝を持っている為に、小径を大径部の溝長まで作りだすことで小径部のステップ長が維持され、再研磨費用の削減が図れます。また面取りと穴あけ、皿もみと穴あけ、ネジ下穴あけ加工を1工程で加工することが可能となります。
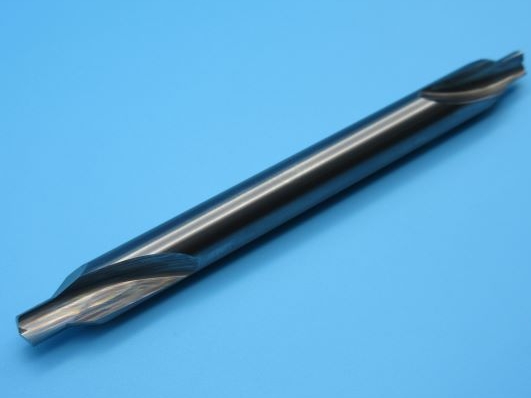
こちらは自動車業界で使用されるサイズがφ10×115のS35C材加工用の両刃センタードリルです。今まで製造していたメーカーが廃業したため、転注先を探しており対応して欲しいとのことでご依頼をいただきました。特殊精密切削工具.comでは当初ご使用いただいていた工具を基に採寸と設計をしたところ、従来品と変わらず使用感の良い工具でお客様にご満足いただけました。本事例のように転注先をお探しの方や海外製工具の製作を依頼する方は少なくありません。当社の場合ですと図面が無くても、サンプル品をお貸しいただければ、同じ寸法、同じ仕様で製作が可能でございますので、ぜひお困りの工具案件がございましたら、お気軽にご連絡ください。
精密切削工具の製作なら特殊精密切削工具.comにお任せ下さい!
今回はドリル刃を精密加工する際のポイントについてご紹介をさせていただきました。ドリルはワークに穴をあける工具であるために、刃先の先端にかかる圧力や熱が残留するために工具の短命化や構成刃先を引き起こします。そのためにも①切れ味と②切粉の排出③求心性の3点を重視した設計が必要となります。
当社では創業から84年以上、お客様のご要望に合わせてオーダーメードの工具を開発・製造してまいりました。お客様それぞれに世界一の究極の逸品の工具を作り上げることをモットーに最先端設備を揃えており、高精度な加工を実現する環境を整えてまいりました。工業界から医療業界と「人体から宇宙まで」幅広く、精度が必要な工具の納品実績が多数ございます。
切削工具にお困りの方は、特殊精密切削工具.comまでお問い合わせください!
最後まで読んでいただき、ありがとうございました!