エンドミルの加工時に起きるトラブルとその対策について
はじめに
機械加工に従事する多くの方々にとって欠かせない切削工具。しかし、切削工具を使用する上で、チッピングや折損、切りくずの詰まり等のトラブルが起きてしまう場合があります。トラブルに対し、最適な対策をしなければ加工コストの増加のみならず、加工品質の低下に繋がりかねません。今回は、エンドミルのトラブルとそれぞれへの対策について説明します。
>>技術コラム『ドリルの加工時に起きるトラブルとその対策について』はこちら
>>技術コラム『リーマの加工時に起きるトラブルとその対策について』はこちら
エンドミルは、どのような工具?
エンドミルとは、外周面及び端面に切れ刃を持つシャンクタイプのフライス工具で、フライス盤やマシニングセンタで使用され、ワークの上面、側面、ポケット、溝等を加工する工具です。エンドミルの形状はドリルとよく似ていますが、ドリルは軸方向に推進し穴をあけるのに対し、エンドミルは軸に直交する方向に移動しながらいろいろな形状を加工をする工具です。
>リーマの基礎知識・各部の名称【切削工具の基礎知識シリーズ】
>ドリルの基礎知識・各部の名称【切削工具の基礎知識シリーズ】
エンドミルに求められることとは?
エンドミルはドリルと異なり、ワークの上面や側面、ポケット、溝などを加工する工具です。そのため、三次元に動かして使用することがほとんどです。その中で求められることは、荒加工時の重切削に強いこと、仕上げ加工時の高い精度、切りくずの処理がスムーズであること(排出性)、切削熱に強いこと(耐熱性)、長期間使用出来ること(高寿命、耐摩耗性)が挙げられます。これらを満たすためには、ワークのことを理解し、仕上がり寸法や使用する機械、ツールパスや加工条件に合わせて設計する必要があります。しかし、誤った設計になっていると、エンドミルが異常摩耗を起こしたり折損してしまったり、またワークを傷つけてしまうと言ったトラブルを起こしてしまいます。
>>技術コラム『エンドミル製作の上で刃数と刃長が重要な理由とは?』はこちら
エンドミルおいて発生するトラブル
エンドミルにおけるトラブルには1.異常摩耗、2.加工面が荒れてしまう、3.切りくずの詰まり、4.バリの発生が挙げられます。それぞれについて説明していきます。
>>よくある質問『エンドミルのトラブルシューティング』はこちら
1.異常摩耗
要因として、被削材に対して工具材質が合っていない、もしくは加工条件が合っていないことが多いです。被削材の硬度と同程度の硬度の工具を使用しても切削することは出来ません。また、工具材質に合った適正な切削速度、送りで加工を行わないと能力以上の仕事をエンドミルにさせてしまい、エンドミルは摩耗してしまいます。対策として、工具材質の見直し、コーティングの付加、加工条件の見直しを行うことで解消できます。
2.加工面が荒れてしまう
むしれなどが発生して加工面粗度が悪い場合には、切削抵抗が大きい、一刃当たりの送りが大きいこと、加工長(深さ)に対して工具径が小さいことなどが考えられます。送りを変えずに刃数を増やす、もしくは切削速度を上げる、切込深さを小さくする、または送り自体を落とすことで面粗度が上がります。アップカットやダウンカットの回転方向を見直すことも考えられます。また、工具の倒れが発生しているがどうしても厳しい条件下での加工になってしまう場合は、エンドミルの首下径・シャンク径を太くすることや、材質を超硬にして剛性を上げることで対策できます。
また、ビビりが発生している場合には、被削材に対する工具剛性の不足と共振を引き起こす加工条件で加工されていることが挙げられます。切削精度を求める場合や切削面の面粗度を求める場合には、芯厚が厚く剛性の高い刃数の多いエンドミルを選定し、工具の突き出し量を最小限に抑えてたわみを抑え適切な切込量で切削することが重要です。また、切削中に発生する振動の抑制の為に、送り量、周速、切込深さを見直すことや、刃を不等角や不等リードにすること、ワークや工具が適正に保持、取付されているかを確認することで対策することも可能です。
3.切りくずの詰まり
溝加工やポケット加工の際に起きる可能性があります。溝加工やポケット加工においては一般的に2枚刃のエンドミルを使用することが多く、その理由は、チップポケットを大きく取って切りくずの排出性を良くするためです。刃数が多いと芯厚が太く、剛性が高くなりますが、切りくずの排出性は悪くなりますので、それぞれの加工方法に適した刃数を選定する必要があります。
4.バリの発生
バリは、塑性変形の残骸であり、完全になくすことは出来ませんが、小さくすることが可能です。バリを小さくするためには、ねじれ角の強いエンドミルを使用して切れ味を上げることや、周速を上げて、送り量を小さくし、切込深さを小さくして塑性変形量を小さくすることが有効です。また、アップカットを採用している場合は加工終わりの出口付近にバリが発生しやすくなるため、加工方法をダウンカットに変更することも考えられます。
切削現場の課題を解決する、東鋼だからこそ可能な特殊エンドミル
エンドミルにおけトラブルを列挙しましたが、2つ以上のトラブルが同時に発生してしまうという方もおられると思います。加えて、現状のトラブルを全て解決しようとすると、何から取り組めば良いか分からなくなってしまいかねません。
このような切削現場の課題を解決する際は、「切削理論」と「材料特性」を熟知している特殊精密切削工具.comにご相談ください。
当社では創業から84年以上、お客様のご要望に合わせてオーダーメードの工具を開発・製造してまいりました。お客様それぞれに世界一の究極の逸品の工具を作り上げることをモットーに最先端設備を揃えており、高精度な加工を実現する環境を整えてまいりました。工業界から医療業界と「人体から宇宙まで」幅広く、精度が必要な工具の納品実績が多数ございます。
加工条件や被削材にあわせて、エンドミルの寿命延長のご提案いたします!
>>特殊エンドミル 開発サービス
特殊エンドミルの工具事例
続いて、実際に当サイトを運営する株式会社東鋼が製作した、特殊エンドミルの工具事例をご紹介いたします。

3枚刃エンドミル
半導体業界で使用されるサイズがφ8×80の超硬製エンドミルです。依頼背景としては、総型エンドミルを新規製作を検討しており、CADデータしか提出できないが、エンドミルの製作は可能かご相談をいただきました。特殊精密切削工具.comではCADデータのみで納入仕様図面を作図し、それを基に刃型形状の設定を行い、総型エンドミルを製作しました。
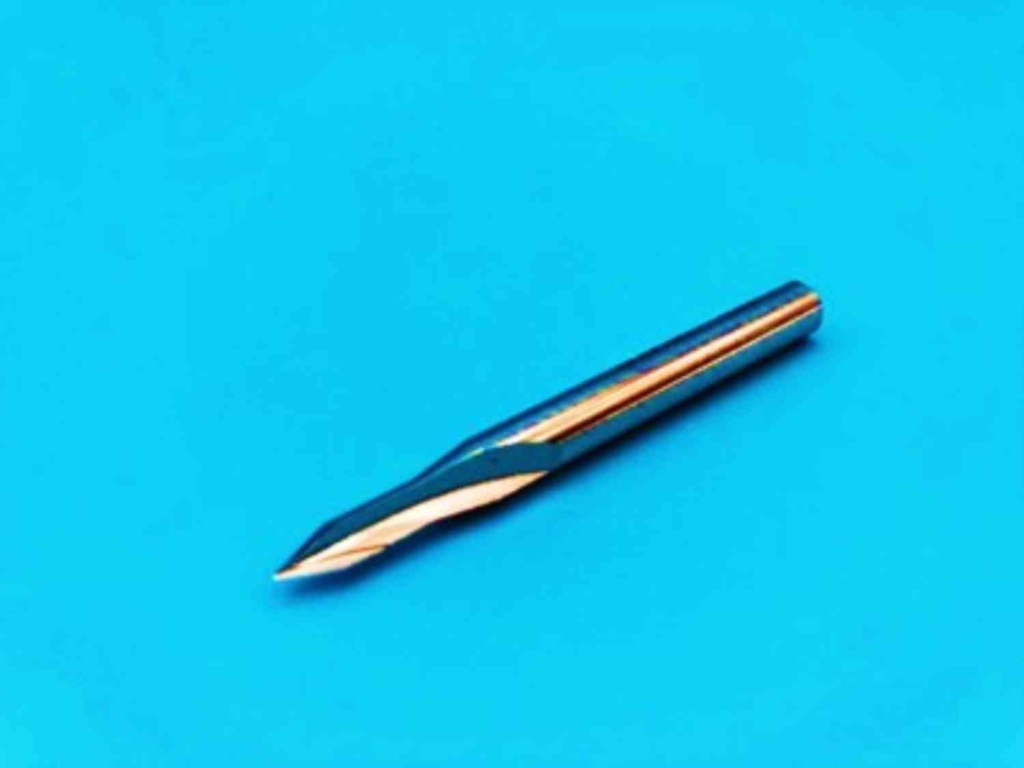
テーパー加工エンドミル
電子機械部品業界で使用されるサイズがφ6×60のハイス製テーパー加工エンドミルです。ご依頼いただいたお客様のご要望として、既存工具ではテーパー部の加工面が楕円に加工されてしまうために新規工具への変更を検討されていました。従来のスクイ角0°のテーパーエンドミルでは切削抵抗が大きいために、当社ではスクイ角を設け切削抵抗を減らした形状を提案し、スクイ角を設けた工具設計により楕円になることを抑えることが出来ました。
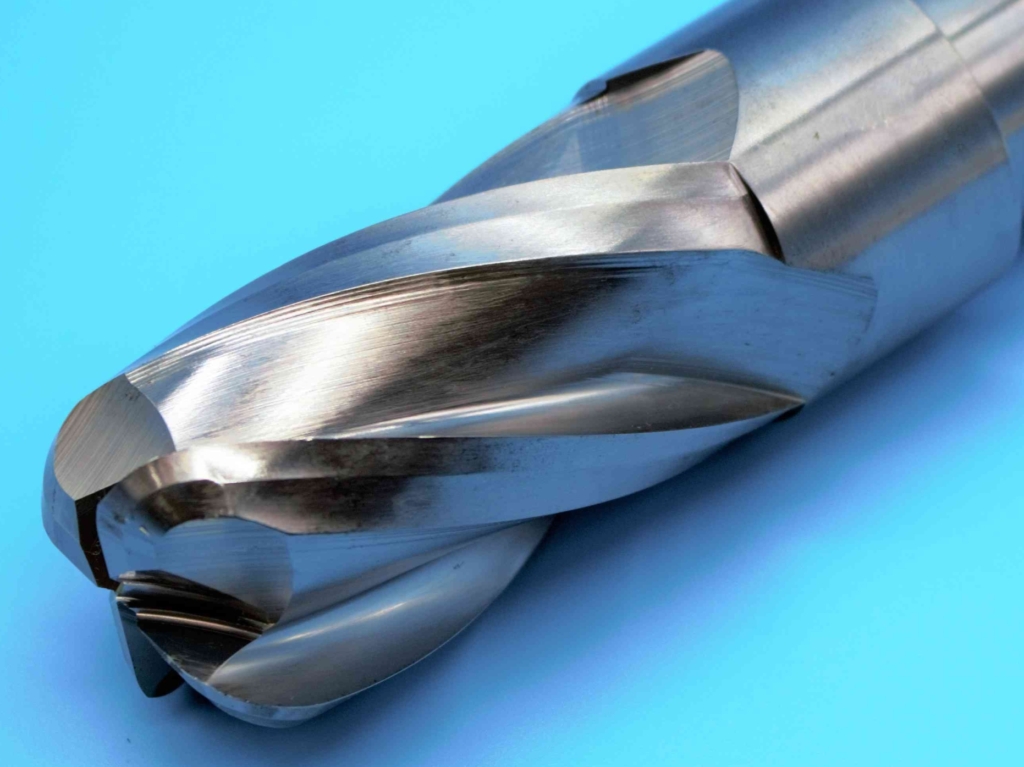
ラジアスエンドミル
ラジアスエンドミルとは、スクエアエンドミルの底刃コーナー部をR状にしたエンドミルをいいます。また、コーナーRエンドミルなどとも呼ばれます。ラジアスエンドミルは切削加工した縦横の面と面の境にRができるためそのような仕上げを求められたときに使用します。また、スクエアエンドミルでコーナーがチッピングし易い時にもラジアスエンドミルを使う事で、コーナーのチッピングを低減させる事が可能です。
トラブルを根本的に解決するためには
軸物工具におけるトラブルを列挙しましたが、2つ以上のトラブルが同時に発生してしまうという方もおられると思います。加えて、現状のトラブルを全て解決しようとすると、何から取り組めば良いか分からなくなってしまいかねません。これを根本的に解決するためには、「切削理論」と「材料特性」を熟知している特殊精密切削工具.comにご相談ください。
当社では創業から84年以上、お客様のご要望に合わせてオーダーメードの工具を開発・製造してまいりました。お客様それぞれに世界一の究極の逸品の工具を作り上げることをモットーに最先端設備を揃えており、高精度な加工を実現する環境を整えてまいりました。工業界から医療業界と「人体から宇宙まで」幅広く、精度が必要な工具の納品実績が多数ございます。
切削工具にお困りの方は、特殊精密切削工具.comまでお問い合わせください!
最後まで読んでいただき、ありがとうございました!